Die Casting: A Crucial Process for Precision Manufacturing in Today's Industries
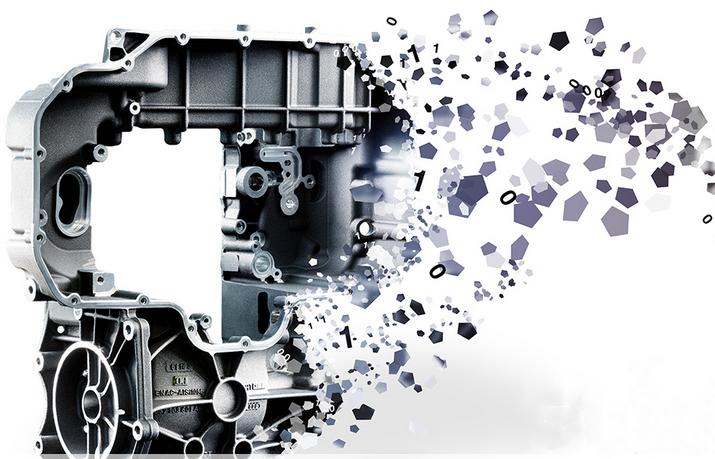
Die casting is a widely used manufacturing technique that has become indispensable in the production of high-precision, complex metal parts across many industries. By injecting molten metal into a mold at high pressure, Role of Die Casting enables the creation of intricate shapes with excellent dimensional accuracy and a smooth surface finish. This process is crucial for mass production of parts with tight tolerances, durability, and performance. In this article, we will explore the significance of die casting, its key benefits, its applications, and its role in advancing manufacturing efficiency.
What is Die Casting?
Die casting is a metal casting process in which molten metal is forced into a mold under high pressure. The metal, typically a non-ferrous alloy like aluminum, zinc, magnesium, or copper, is injected into a precisely designed mold cavity. Once the metal cools and solidifies, it forms a part that precisely matches the shape of the cavity, with minimal need for post-processing.
The molds, or dies, used in the die casting process are made from high-quality, durable steel to withstand the high pressures and temperatures involved. This process is particularly advantageous for creating large volumes of parts with complex shapes, fine details, and high-quality surface finishes.
Key Advantages of Die Casting
Die casting provides several benefits that make it a go-to process in modern manufacturing, especially for industries that require high-volume production of metal parts. Some of the key advantages of die casting include:
1. High Precision and Dimensional Accuracy
One of the most significant advantages of die casting is its ability to produce parts with exceptional precision and tight tolerances. The high pressure involved in the casting process forces the molten metal to fill the mold cavity completely, ensuring minimal variation between parts. This allows manufacturers to produce components that are nearly identical in size and shape, making it ideal for applications that demand high dimensional accuracy.
The precision of die casting helps reduce the need for additional machining or finishing, thus reducing costs and lead times for manufacturers. This is especially beneficial in industries where even the smallest deviations in part size can affect the functionality of the product, such as in the automotive or electronics sectors.
2. Cost-Effective for High-Volume Production
Die casting is highly cost-effective, particularly for high-volume production runs. While the initial cost of designing and producing the die may be high, the cost per part significantly decreases as production volumes increase. Once the die is made, parts can be produced rapidly and efficiently with minimal material waste, making it an attractive option for large-scale manufacturing.
For industries that require the production of thousands or even millions of identical parts, such as automotive and consumer electronics, die casting provides a highly efficient and cost-effective solution. The speed of production and the reduction in material waste ensure that die casting remains one of the most cost-efficient processes for large production runs.
3. Ability to Create Complex Geometries
Die casting excels at creating parts with intricate shapes and complex geometries. The high pressure used in the process ensures that even fine details, sharp edges, and deep cavities are captured accurately in the final part. This capability is particularly beneficial in industries like automotive, aerospace, and electronics, where parts often require complex internal structures or detailed surfaces.
The ability to produce parts with such intricate geometries allows manufacturers to design components that would be difficult or impossible to produce using other methods, such as machining or forging. Moreover, die casting can produce parts with thin walls, contributing to weight reduction without sacrificing strength, making it ideal for industries that prioritize lightweight yet durable materials.
4. Superior Surface Finish
Die-cast components typically have a smooth surface finish, reducing the need for post-processing treatments like polishing, painting, or sanding. In many cases, die-cast parts can be used directly after casting, or only require minor finishing to meet final specifications. This reduces labor costs and time spent on additional surface treatments, making die casting a more efficient manufacturing process.
The smooth surface finish is particularly beneficial in industries where aesthetics or high-quality finishes are essential, such as in the production of consumer electronics, automotive parts, and decorative goods.
5. Material Flexibility
Die casting is compatible with a wide variety of metals, which allows manufacturers to select the most suitable material for their specific needs. The most commonly used materials in die casting are:
- Aluminum: Known for its lightweight properties, corrosion resistance, and strength-to-weight ratio. Aluminum is widely used in automotive, aerospace, and electronics applications.
- Zinc: Provides excellent fluidity, strength, and dimensional stability. Zinc is ideal for small, precise components used in automotive and electronics applications.
- Magnesium: The lightest of all structural metals, magnesium is often used in automotive and aerospace industries to reduce weight while maintaining strength.
- Copper Alloys: Die-cast copper alloys, such as brass and bronze, offer high corrosion resistance and durability, making them ideal for electrical applications and components exposed to harsh environments.
This variety of materials allows manufacturers to choose the metal that best suits the performance, cost, and durability requirements of the final product.
Applications of Die Casting in Various Industries
Die casting is used in a broad range of industries due to its ability to produce high-quality, precise components in large volumes. Here are some key applications of die casting across various sectors:
1. Automotive Industry
The automotive industry is one of the largest consumers of die-cast parts. Many automotive components, such as engine blocks, transmission housings, cylinder heads, wheels, and chassis parts, are made using die casting. Aluminum and magnesium alloys are particularly popular in automotive applications due to their lightweight properties, which help improve fuel efficiency and reduce vehicle weight.
Die casting also allows manufacturers to create parts with intricate shapes, reducing the number of components and assembly steps required in vehicle production. This streamlines the manufacturing process and reduces overall costs.
2. Aerospace Industry
In aerospace, where weight reduction and high performance are essential, die casting plays a crucial role in producing lightweight yet strong components. Die-cast parts are commonly used for structural brackets, housings, and engine components in the aerospace industry. Aluminum and magnesium alloys are frequently chosen for their excellent strength-to-weight ratios and resistance to corrosion.
The precision and ability to create complex geometries make die casting an ideal choice for producing aerospace parts, where tight tolerances and reliability are critical.
3. Electronics Industry
Die casting is extensively used in the electronics industry for producing parts such as housings, connectors, heat sinks, and enclosures. The ability to create intricate shapes with high precision is essential in the production of small, compact components used in modern electronic devices.
Aluminum is often the material of choice in electronics due to its excellent thermal conductivity and ability to dissipate heat effectively, which is critical for protecting sensitive electronic components from overheating.
4. Consumer Goods and Appliances
Many consumer goods and household appliances benefit from die casting, which provides an efficient way to produce high-quality, durable parts. Items such as power tools, kitchen appliances, lighting fixtures, and furniture hardware often feature die-cast components. The speed of production and ability to achieve fine details makes die casting a perfect choice for producing these types of products.
5. Medical Devices
The medical device industry also relies on die casting to produce durable and accurate components. From housings for diagnostic equipment to surgical instruments, die-cast parts are commonly used in medical devices due to their reliability, precision, and strength. The high level of quality control in die casting ensures that these components meet the rigorous standards required for medical applications.
The Future of Die Casting
The die casting industry continues to evolve with advancements in technology and manufacturing techniques. Some trends that are shaping the future of die casting include:
1. Automation and Digitalization
The use of automation and digital technologies in die casting is increasing. Robotics and computer-controlled machines are enhancing production speed and precision, while advanced sensors and monitoring systems are improving quality control. Automation is helping manufacturers reduce labor costs, minimize human error, and increase overall efficiency.
2. Sustainable Manufacturing
As environmental concerns continue to grow, the die casting industry is focusing on sustainability. Manufacturers are looking for ways to reduce energy consumption, minimize waste, and use recycled materials in the die casting process. Advances in materials, such as recycled aluminum and zinc, are contributing to a more sustainable manufacturing process.
3. Advanced Materials and Alloys
New materials and alloys with improved properties are being developed to meet the demands of modern industries. These materials offer enhanced performance, such as better heat resistance, corrosion resistance, and strength. As technology advances, die casting will continue to adapt to accommodate these new materials.
Conclusion
Die casting plays an essential role in modern manufacturing by providing a cost-effective, efficient, and precise method for producing high-quality metal components. Its ability to create complex shapes with tight tolerances, reduce waste, and offer material flexibility makes it a preferred choice in a wide range of industries, including automotive, aerospace, electronics, and medical devices. As the manufacturing landscape evolves, die casting will continue to advance, driven by technological innovations and increasing demands for sustainability and precision.
- Art
- Causes
- Crafts
- Dance
- Drinks
- Film
- Fitness
- Food
- Игры
- Gardening
- Health
- Главная
- Literature
- Music
- Networking
- Другое
- Party
- Religion
- Shopping
- Sports
- Theater
- Wellness
