Submerging Success: An Exploration of Pipeline Weight Bags
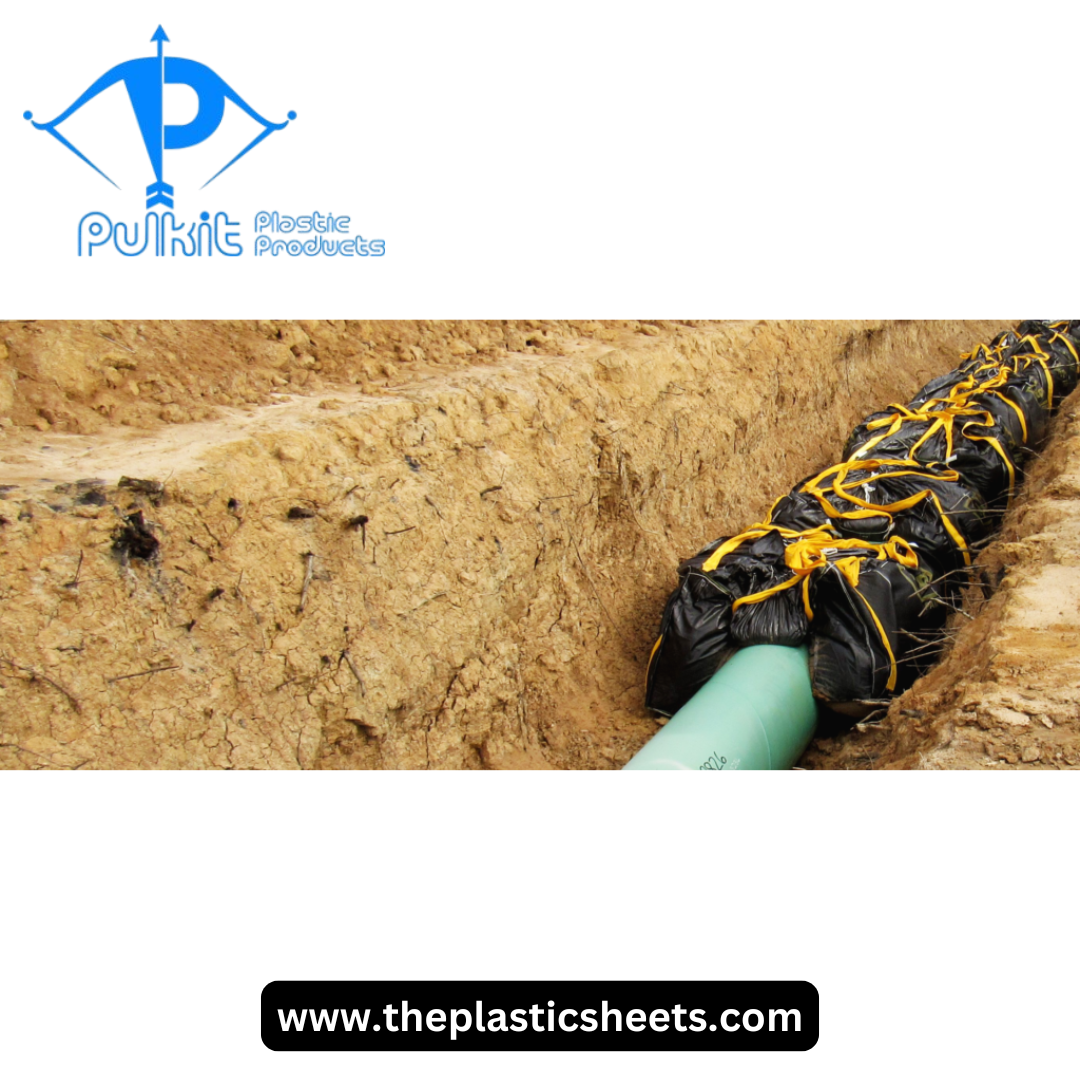
Pipeline weight bags, also known as ballast bags, are essential tools in the oil and gas industry, specifically designed to provide the necessary stability and buoyancy control for pipelines during underwater installation and operation. These heavy-duty bags are strategically placed along the pipeline to counteract the buoyancy force exerted by the water and prevent movement. Their effectiveness is critical for ensuring the safe and efficient transportation of oil and gas across diverse underwater terrains. Understanding their construction, applications, and importance is vital in comprehending the complex world of subsea infrastructure. This Pulkit Plastic Products explores the multifaceted world of pipeline weight bags, their applications, and their significance in modern pipeline projects. We will delve into the specifics of weight bag in India, the various types of pipeline weight bags, and the role of river weights for pipelines.
Construction and Materials of Pipeline Weight Bags
Pipeline weight bags are typically constructed from high-strength, durable fabrics such as polyester, nylon, or other synthetic materials. These fabrics are coated with a robust polyurethane or PVC layer to provide exceptional resistance to abrasion, tearing, and the harsh marine environment. The bags are designed with heavy-duty lifting loops or straps to facilitate safe handling and deployment underwater. They usually incorporate robust closing mechanisms such as zippers, flaps, or tie-down systems to contain the weight material securely.
The weight material itself can vary depending on the project requirements. Common filling materials include: sand, gravel, or concrete. The selection of the weight material depends on factors such as the desired density, the environmental conditions, and the available resources. Sand and gravel are often used for shallower water depths, while concrete provides a denser option for deeper applications. Weight bags are designed to be easily filled and emptied, simplifying the process of adding or removing weight as needed during pipeline installation and maintenance. This flexibility enables the precise adjustment of buoyancy.
Applications and Uses of Pipeline Weight Bags
The primary application of Weight bag in India is to provide stability and control buoyancy during the installation of underwater pipelines. They are critical for preventing pipelines from floating to the surface or moving laterally due to currents, waves, or other external forces. The bags are strategically placed along the pipeline at predetermined intervals, ensuring even weight distribution and maintaining the pipeline's position on the seabed.
Beyond the installation phase, pipeline weight bags also serve vital functions throughout the operational life of the pipeline. They can be used to provide additional weight and stability to the pipeline, particularly in areas with strong currents or unstable seabed conditions. During maintenance and repair operations, weight bags can be employed to temporarily secure sections of the pipeline while they are being inspected, repaired, or replaced. These bags are also deployed in various marine environments, including coastal waters, rivers, and deep-sea locations. Considering their multiple uses, weight bag in India is very beneficial.
Types of Pipeline Weight Bags and Their Characteristics
There are various types of pipeline weight bags, each designed to meet specific project requirements. Standard weight bags are typically rectangular or square-shaped bags filled with sand, gravel, or concrete. They offer a cost-effective solution for many applications. Custom weight bags can be designed and fabricated to fit specific pipeline configurations and project needs. These bags may have unique shapes, sizes, and features, such as integrated lifting points or specialized closure systems.
Another category includes adjustable weight bags, which allow for precise control of the weight and buoyancy. These bags often feature compartments or sections that can be filled or emptied independently, enabling adjustments to be made underwater. Rock bags are specially designed for use in areas with rocky or uneven seabed conditions. They often have reinforced construction and durable materials to withstand the abrasive environment. These can be useful in situations where river weights for pipelines are used.
Installation and Deployment of Pipeline Weight Bags
The installation and deployment of Pipeline weight bags require specialized equipment and trained personnel. The bags are typically lifted from the surface using cranes or other lifting devices and lowered into the water. Divers or remotely operated vehicles (ROVs) are often used to position the bags accurately and secure them to the pipeline. The deployment process must be carefully planned and executed to ensure the safe and efficient installation of the bags.
Before deployment, the pipeline route must be surveyed to identify any potential hazards or obstacles. The weight bag placement is then determined based on factors such as the pipeline's diameter, the water depth, the soil conditions, and the hydrodynamic forces acting on the pipeline. Precise calculations are performed to determine the required weight and distribution of the weight bags. The deployment process is also governed by strict safety regulations, including the use of personal protective equipment and the implementation of emergency procedures.
The Importance of River Weights for Pipelines
River weights for pipelines are a specialized type of weight bag designed for use in river environments. These bags are typically made from durable materials, such as heavy-duty geotextiles, and filled with dense materials, such as concrete or iron ore. They provide the necessary weight to counteract the buoyancy of the pipeline, preventing it from floating or moving in the river currents.
The use of river weights is particularly critical for pipelines that cross rivers or other bodies of water. The weights help to maintain the pipeline's position, protecting it from damage caused by erosion, scouring, or other environmental factors. They also contribute to the stability of the pipeline, ensuring its safe and reliable operation. River weights for pipelines are carefully designed and installed to minimize their impact on the river ecosystem.
Benefits and Advantages of Pipeline Weight Bags
Pipeline weight bags offer several advantages over alternative methods of pipeline stabilization. They are a cost-effective solution compared to other methods, such as concrete coating or trenching. They are also flexible and adaptable, allowing for the adjustment of weight and buoyancy as needed. Weight bags can be easily transported and deployed, and they can be used in a variety of environments, including deep-sea locations, coastal waters, and river systems.
They are also environmentally friendly since they can be removed and reused if necessary. The use of pipeline weight bags minimizes disruption to the seabed and the marine environment. They offer a reliable and proven solution for ensuring the stability and safe operation of underwater pipelines. These versatile bags are essential for the safe laying and long-term operation of pipelines worldwide.
Conclusion
The River weights for pipelines are indispensable tools in the oil and gas industry, critical for the installation, stability, and maintenance of underwater pipelines. Their diverse applications, customizable designs, and cost-effectiveness make them a preferred solution for a wide range of subsea projects. The use of carefully designed and deployed weight bags ensures the safe and efficient transportation of oil and gas across diverse underwater environments, contributing significantly to the global energy supply. From the needs of the weight bag in India to the applications for river weights for pipelines, their impact is felt worldwide.
Frequently Asked Questions
-
How long do pipeline weight bags last?
The lifespan of pipeline weight bags depends on several factors, including the materials used, the environmental conditions, and the frequency of use. High-quality bags, made with durable materials, can last for many years.
-
What is the maximum water depth for using pipeline weight bags?
Pipeline weight bags can be used in a wide range of water depths, from shallow coastal waters to the deep ocean. The maximum water depth depends on the design of the bag, the filling material, and the lifting equipment.
-
Can pipeline weight bags be reused?
Yes, pipeline weight bags can often be reused, provided they have not been damaged or compromised. The reusability of the bags depends on their construction, the materials used, and the operating conditions.
-
How are the weight and buoyancy of the bags calculated?
The weight and buoyancy calculations are performed based on the pipeline's diameter, the water depth, the soil conditions, and the hydrodynamic forces acting on the pipeline. These calculations are crucial to determine the required size, weight, and placement of the bags.
- Art
- Causes
- Crafts
- Dance
- Drinks
- Film
- Fitness
- Food
- Παιχνίδια
- Gardening
- Health
- Κεντρική Σελίδα
- Literature
- Music
- Networking
- άλλο
- Party
- Religion
- Shopping
- Sports
- Theater
- Wellness