The Importance of Quality Control in Core Cutting Line Operations
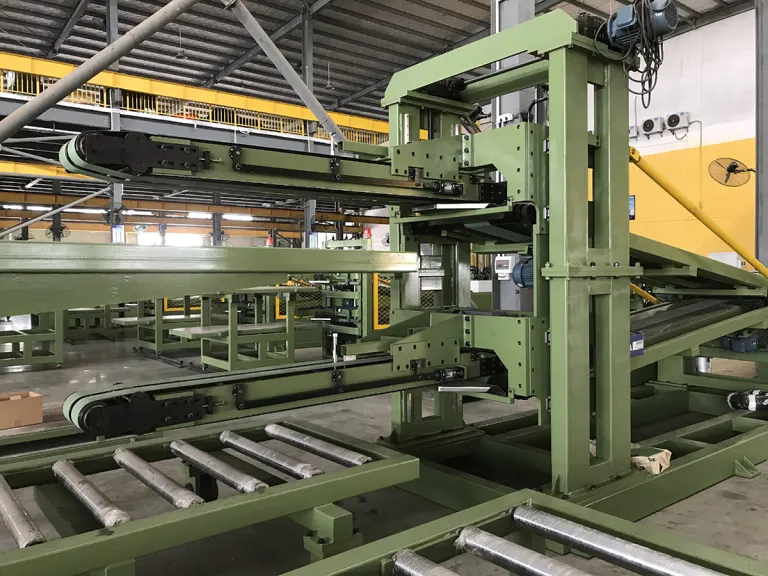
Quality control is a critical aspect of any manufacturing process, and core cutting line operations are no exception. The production of high-quality cores is essential for the efficient operation of electrical core slitting machine , and any defects or irregularities in the core can have significant consequences. In this article, we will explore the importance of quality control in core cutting line operations, highlighting the benefits of implementing a robust quality control system and the potential consequences of neglecting this critical aspect of production.
The Role of Quality Control in Core Cutting Line Operations
Quality control plays a vital role in ensuring that the cores produced by a cutting line operation meet the required specifications and standards. This involves monitoring and controlling various parameters, such as the dimensions, shape, and material properties of the core, to ensure that they conform to the design requirements. Quality control also involves identifying and addressing any defects or irregularities that may arise during the production process, such as cracks, burrs, or other surface imperfections. By implementing a robust quality control system, manufacturers can ensure that their cores meet the highest standards of quality and reliability.
Benefits of Implementing Quality Control in Core Cutting Line Operations
Implementing a quality control system in core cutting line operations offers numerous benefits, including improved product quality, reduced waste, and increased efficiency. By monitoring and controlling the production process, manufacturers can identify and address any defects or irregularities early on, reducing the likelihood of costly rework or scrap. Quality control also helps to ensure that the cores produced meet the required specifications and standards, reducing the risk of non-conformance and the associated costs. Furthermore, a robust quality control system can help to improve customer satisfaction, as high-quality cores are essential for the efficient operation of electrical transformers.
Consequences of Neglecting Quality Control in Core Cutting Line Operations
Neglecting quality control in core cutting line operations can have significant consequences, including reduced product quality, increased waste, and decreased efficiency. Without a robust quality control system in place, manufacturers may produce cores that do not meet the required specifications and standards, leading to costly rework or scrap. In addition, neglecting quality control can lead to a higher risk of non-conformance, which can result in costly penalties and damage to the manufacturer's reputation. Furthermore, poor-quality cores can lead to reduced customer satisfaction, as they may not perform as expected, leading to reduced sales and revenue.
Key Elements of a Quality Control System in Core Cutting Line Operations
A quality control system in core cutting line operations should include several key elements, including inspection and testing, process control, and corrective action. Inspection and testing involve monitoring the production process to ensure that the cores produced meet the required specifications and standards. Process control involves adjusting the production process to prevent defects or irregularities from occurring. Corrective action involves addressing any defects or irregularities that do occur, to prevent them from affecting the quality of the final product. By incorporating these elements, manufacturers can ensure that their quality control system is robust and effective.
Best Practices for Implementing Quality Control in Core Cutting Line Operations
Implementing a quality control system in core cutting line operations requires careful planning and execution. Best practices include establishing clear quality objectives, defining quality control procedures, and training personnel on quality control procedures. Manufacturers should also establish a system for monitoring and controlling the production process, including inspection and testing, process control, and corrective action. Furthermore, manufacturers should continually review and improve their quality control system, to ensure that it remains effective and efficient.
Conclusion
In conclusion, quality control is a critical aspect of core cutting line operations, essential for ensuring that the cores produced meet the required specifications and standards. By implementing a robust quality control system, manufacturers can improve product quality, reduce waste, and increase efficiency. Neglecting quality control can have significant consequences, including reduced product quality, increased waste, and decreased efficiency. By incorporating key elements, such as inspection and testing, process control, and corrective action, manufacturers can ensure that their quality control system is robust and effective. By following best practices, manufacturers can establish a quality control system that meets their needs and ensures the production of high-quality cores
- Art
- Causes
- Crafts
- Dance
- Drinks
- Film
- Fitness
- Food
- الألعاب
- Gardening
- Health
- الرئيسية
- Literature
- Music
- Networking
- أخرى
- Party
- Religion
- Shopping
- Sports
- Theater
- Wellness