3D Printing Plastics Market Analysis and Forecasts, 2024-2032
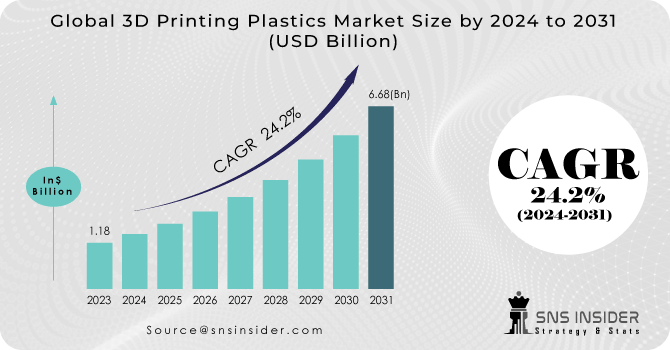
3D printing plastics are a vital component in the additive manufacturing (AM) process, used for creating intricate and functional objects layer by layer. These plastics, available in various formulations, offer diverse properties to cater to a wide range of applications across industries like automotive, aerospace, healthcare, consumer goods, and more. Commonly used 3D printing plastics include polylactic acid (PLA), acrylonitrile butadiene styrene (ABS), polycarbonate (PC), and nylon, among others. Each of these materials is selected based on specific needs such as strength, flexibility, durability, or ease of use in different printing technologies. The ability to print customized, complex designs with 3D printing plastics has revolutionized product development, prototyping, and manufacturing processes, providing significant cost savings, speed, and design freedom. As industries continue to explore new ways to leverage additive manufacturing, the demand for specialized 3D printing plastics is set to grow exponentially.
The 3D Printing Plastics Market size was valued at USD 1.18 billion in 2023 and is supposed to reach USD 6.68 billion by 2031 and develop at a CAGR of 24.2% over the forecast period 2024-2031.
Future Scope
The future scope of 3D printing plastics is marked by advancements in material science and the increasing integration of 3D printing technologies across industries. As manufacturers seek to streamline production processes and enhance product performance, the demand for advanced 3D printing plastics with specific material properties—such as heat resistance, higher tensile strength, and chemical resistance—will continue to rise. Moreover, there is a significant opportunity for bioplastics and environmentally friendly 3D printing plastics, as sustainability becomes a priority in industrial processes. The integration of 3D printing with other technologies like artificial intelligence and robotics will further accelerate innovation in plastic materials, leading to the development of more efficient and versatile 3D printing plastics. With applications expanding from rapid prototyping to the production of end-use parts, the role of 3D printing plastics in industries such as automotive, healthcare, and consumer products will only increase.
Emerging Trends
Several key trends are shaping the 3D printing plastics market. One of the most significant trends is the growing shift toward bio-based and biodegradable plastics in 3D printing. As sustainability becomes a greater focus, consumers and manufacturers are opting for materials like PLA, which is derived from renewable resources and can be composted. Another important trend is the development of high-performance materials designed for specific applications, such as carbon fiber-reinforced filaments for increased strength and heat resistance, or elastomers for producing flexible parts. The rise of multi-material 3D printing, which allows different plastics to be combined in a single print job, is also gaining momentum, enabling the production of more complex and functional parts. Additionally, advancements in 3D printing technologies, such as direct energy deposition and powder bed fusion, are pushing the boundaries of material possibilities, allowing for higher precision and greater versatility in the types of plastics that can be used.
Drivers
The market for 3D printing plastics is primarily driven by the increasing adoption of additive manufacturing in various industries. The ability to produce highly customized, complex, and lightweight parts at reduced costs is a significant factor driving demand. In the automotive and aerospace sectors, where weight and material properties are critical, 3D printing plastics allow for the creation of parts that would be difficult or impossible to manufacture using traditional methods. Additionally, the rise of personalized healthcare, where customized medical devices, implants, and prosthetics are increasingly in demand, is also contributing to market growth. The cost-effectiveness of 3D printing plastics for rapid prototyping, short-run production, and on-demand manufacturing further accelerates their use across industries. Furthermore, the shift toward more sustainable manufacturing practices, including the use of eco-friendly and recyclable plastics, is boosting the demand for 3D printing materials that align with these objectives.
Restraints
Despite the promising growth prospects, the 3D printing plastics market faces several challenges. One of the main limitations is the relatively high cost of some specialized 3D printing plastics, particularly those with advanced material properties such as high strength, durability, or thermal resistance. The expense of these materials may be prohibitive for small-scale manufacturers or startups. Additionally, while 3D printing offers significant design flexibility, the materials currently available are still limited in terms of performance compared to traditional manufacturing materials, especially for applications requiring high strength, extreme temperature resistance, or electrical conductivity. Another constraint is the limited availability of 3D printers capable of using certain types of advanced plastics, which restricts the widespread adoption of these materials. Furthermore, the relatively slow production speeds of some 3D printing processes may not be suitable for large-scale manufacturing, limiting the potential for mass production with 3D printing plastics.
Key Points
· 3D printing plastics are crucial in the additive manufacturing process, offering diverse material options for various industries.
· The demand for advanced 3D printing plastics is driven by the need for high-performance, customized, and cost-effective manufacturing solutions.
· Emerging trends include the shift toward biodegradable plastics, development of high-performance materials, and advancements in multi-material 3D printing.
· Key drivers of growth include the increasing adoption of 3D printing in automotive, aerospace, and healthcare, as well as the shift toward sustainable manufacturing.
· Challenges include the high cost of specialized materials, limited material performance compared to traditional methods, and the slower production speeds of 3D printing technologies.
As 3D printing technology continues to evolve, the plastics used in these processes are expected to become more versatile, sustainable, and affordable. With a growing emphasis on customized solutions, sustainability, and performance, 3D printing plastics will play an integral role in shaping the future of manufacturing across a variety of industries.
Get Free Sample Copy @ https://www.snsinsider.com/sample-request/2552
Contact Us:
Akash Anand – Head of Business Development & Strategy
Phone: +1-415-230-0044 (US) | +91-7798602273 (IND)
- Art
- Causes
- Crafts
- Dance
- Drinks
- Film
- Fitness
- Food
- Games
- Gardening
- Health
- Home
- Literature
- Music
- Networking
- Other
- Party
- Religion
- Shopping
- Sports
- Theater
- Wellness